Powder metallurgy gears continue to reduce noise and provide operational reliability for electric power tools.
Neglected noise at work
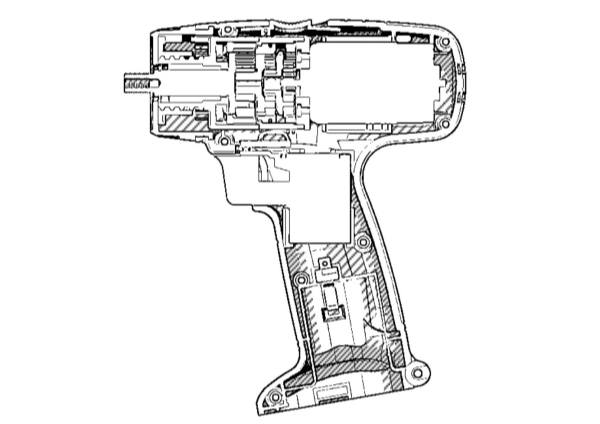
In recent years, people’s interest in DIY is full of enthusiasm, power tools are widely used, both industry and home are a large number of applications of power tools, at present, about 80% of households have power tools, in the process of using power tools, noise pollution is easy to be ignored, in fact, it is a very important issue, the time of the noise will have an impact on the health and the surrounding environment, in order to reduce the hazards caused by the noise, Osweypm engineers and power tool manufacturers have been exploring how to minimise the noise, and to try to increase the durability and reliability of it.
Sources of power tool noise
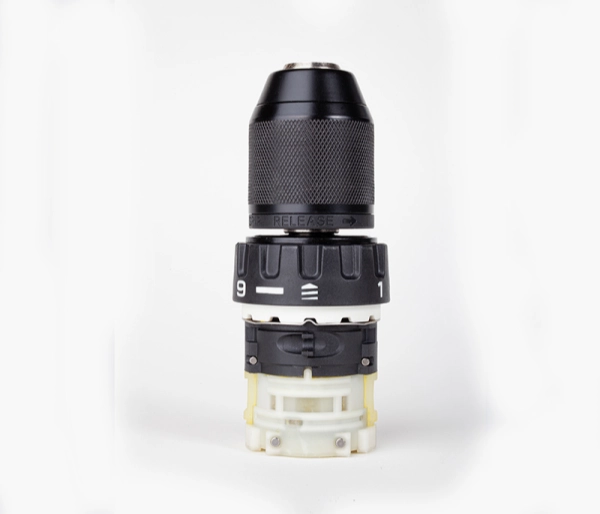

The gearbox of power tools consists of motor, bearings and gears, and the biggest source of noise is the bearings and gears, the traditional production process is to use casting method to manufacture gears, there are internal density and organisation is not uniform, which leads to the production of gears in the use of heat, rapid wear and noise, and the gears manufactured by powder metallurgy have a higher density and uniform internal organisation, and at the same time gears have a very smooth surface finish, which can greatly reduce the noise of the power tools, and take into account the excellent abrasion resistance and impact resistance.
New Materials & Process Control
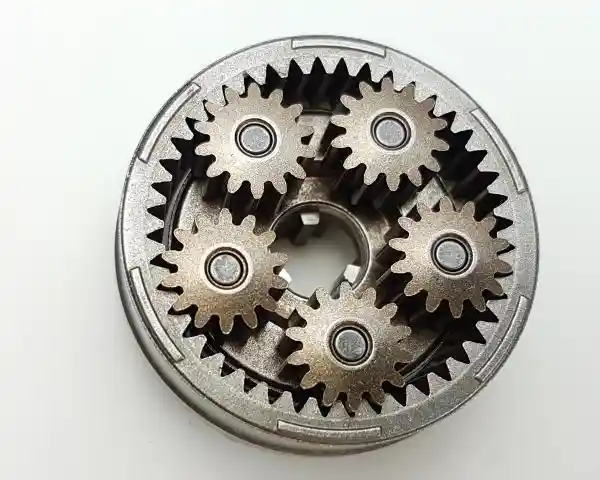
The reliability of power tools is the test of gears and bearings, while maintaining maximum power and torque, but also to ensure the service life and reliability of continuous operation, these requirements are the fundamental gearbox components, which requires the gear manufacturing industry to continue to carry out technological innovation, the use of new combinations of materials and new technologies to improve the physical properties of gears, and at the same time, the quality of the production process is critical to control, and ultimately, make the Sintered gears have better wear resistance, impact resistance and self-lubricating function, which our engineers have been exploring.
Reducing noise helps to protect the surrounding environment, but also protects the health of power tool users, using more environmentally friendly materials to manufacture products that meet safety indicators, which is in sync with environmental sustainability, and has always been the concept of our manufacturing.
Methods of reducing or eliminating noise:
- Use special lubricant when manufacturing the gearbox, increase the surface lubrication area, and design a reasonable position for storing lubricant inside the gearbox.
- In the metal powder added to contain self-lubricating materials, when the lubricant inside the power tool is consumed, there is a self-lubricating function of powder metallurgy gears can reduce the noise generated by friction, and the power of the power tool will not be reduced very quickly.
- Produce gears with higher density and smoother surface to reduce the friction, which can reduce the noise and enhance the torque of the power tools.
- Wear special headphones when using power tools to protect the user’s health.