The pressing process of powder metallurgy involves pressing a material in powdered state into a specified shape by means of a press, just as flour is poured into a mold to make bread. The powder is pressed into a mold and under the high pressure of the press, the metal particles combine to form a workpiece of uniform geometry. Different sizes of presses are used for different powders, depending entirely on the type of material.
Metal powders are added with suitable proportions of lubricants and binders. The powders create friction when pressed, and the addition of lubricants reduces resistance and allows for a more even distribution of particles. The binder is used to temporarily bond the powder with each other in order to facilitate the maintenance of a certain shape in the sintering furnace. However, the pressed workpiece is very fragile and will break easily, so it is important to avoid vibration and extrusion of workpieces on each other during the transport of pressed workpieces to the sintering furnace. This is done to ensure that the sintered dimensions and appearance meet the requirements.
The pressing process is an important step in powder metallurgy and determines the dimensions, surface roughness, and physical properties of the product.
Powder metallurgy is prone to defects when pressing raw blanks:
1. The internal density of the pressed workpiece is unqualified.
The density of the workpiece directly determines its physical and mechanical properties. The higher and more uniform the density, the stronger the mechanical properties of the workpiece. In powder metallurgy, the density and organization inside the billet determine the quality of the finished product. Therefore, for different sizes of parts, the appropriate press should be used to ensure that the density of the pressed workpiece meets the technical requirements. The density of the workpiece should be detected after the completion of the pressing, and it should meet the customer’s requirements before the sintering process.
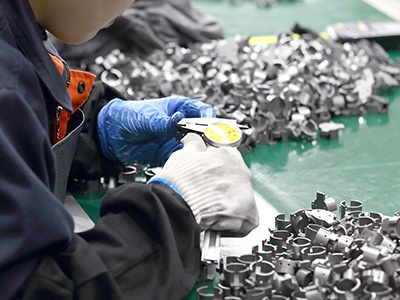
2. Unqualified dimensions of the workpiece after pressing.
This may be a case where the density of the material is not up to standard and should be replaced with the correct metal powder material. Another possibility is that there is an error in the design and manufacture of the mold, which results in the dimensions of the pressed part not being in accordance with the drawing, and the mold tooling should be modified.
3. Failure of the surface of the workpiece
After pressing, the surface of the workpiece has a large number of burrs,the finish is not sufficient to meet the application standards. Remedial measures should be added through secondary processing, but this will also increase the processing cost. Additionally, there are workpieces with missing corners and cracks, which are fatal defects,these errors commonly occur in the powder metallurgy pressing process, resulting in the workpiece being scrapped.