Innovative metal injection molding technology,freedom to cope with complex shapes.
Metal injection molding (MIM) process technology is capable of producing metal parts with complex shapes and high precision. It offers a maximum strength and precision with a density of 99.2%, ensuring no porosity. Additionally, MIM provides a good surface finish and allows for large-scale manufacturing. It is widely used in automotive, medical devices, electronic products, smart home, transmission drive, gardening, aerospace and other fields, and has become an important manufacturing process for modern sintered metal.
Metal Injection Molding Process
Metal Injection Molding (MIM) process is an advanced powder metallurgy technology that combines plastic injection molding and powder metallurgy processes.
Metal Injection Molding mixes metal powder with a polymer binder in a scientifically defined ratio and then injects it into a mold through the injection molding process, where it is formed into a fixed-shaped part. The binder and other impurities are removed through degreasing and high-temperature sintering, and the metal powder is sintered to form a solid metal part that meets a high level of precision and a robust appearance.
Step 1:Process Introduction
Metal Injection Molding (MIM) is the scientific outcome of continuous innovation in metal manufacturing technology, which combines two distinct processes (plastic injection molding and powder metallurgy) into one. This technique allows project designers to overcome free from traditional shape limitations and create design and manufacture metal parts of any geometry with exceptional mechanical properties and high precision. By utilizing plastic molding, MIM enables the production of low -cost, shaped stainless steel, nickel, iron, copper, titanium , and other all-metal parts are obtained by plastic molding , providing greater design flexibility compared to numerous other manufacturing processes.
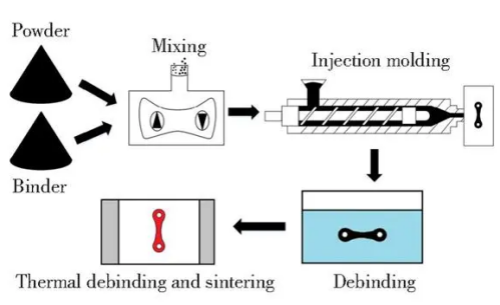
Step 2:Technical Assessment
A team of experienced specialists will work closely with you to determine if the metal part is suitable for the MM process in terms of cost, material and manufacturing feasibility. At the same time, Osweypm experts will also recommend design changes to achieve the lowest cost and best performance through MIM.
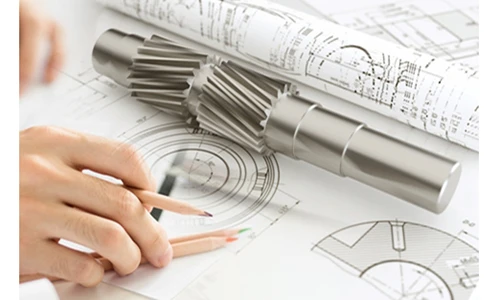
Step 3: Materials Manufacturing
Mixing is the process of combining the metal powder with the binder to achieve uniform particles. The mixing process is conducted in specialized equipment that is heated to a specific temperature, causing the binder to melt. The mixing ratio holds great significance as it determines the mechanical properties of the metal injection-molded parts, considering the nature of the particles.
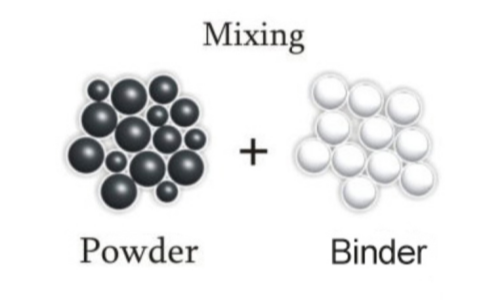
Step 4:Metal Injection
The granular raw material is heated in the machine and injected under high pressure into the mold cavity, where it is injection molded into a “green part”, which is cooled and shaped under controlled conditions until it is released from the mold cavity to form a complex shaped “green part”.
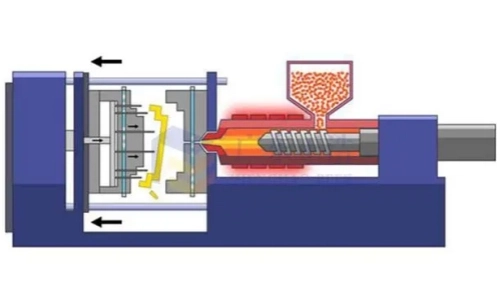
Step 5:Degreasing Technology
Degreasing is a process unique to metal powder injection molding. It involves the process of removing the binder from the raw part, resulting in a brown part is obtained . The degreasing process eliminates around 30-50% of the binder from the blank, leaving 50-70% to provide support for the part in the sintering furnace.
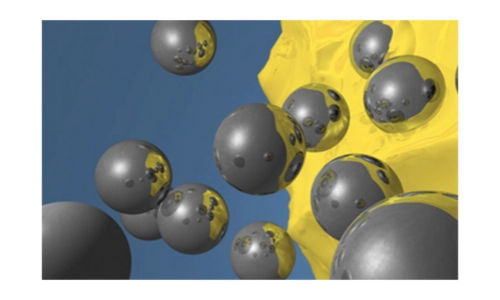
Step 6:Metal Sintering
In the vacuum furnace of the MIM, the binder and other impurities are removed , and the metal powder is densified at temperatures close to the melting point (2700 Fahrenheit scale) to form a complete metal structure . The sintered metal part is then cooled down to obtain its finished form. During this process, finished form, the gaps between the particles disappear due to the fusion of the particles, ultimately achieving the required density and hardness.Once the parts are sintered, they can be applied directly to the project without any additional machining.
Sintering Process:
1.Video Link: Sintering process in the manufacture of metal parts
2.Link: Why are powdered metal parts sintered?
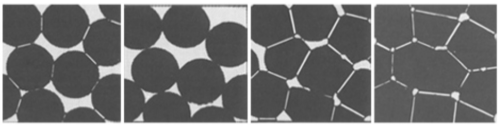
Learn about the cost-effective powder metallurgy process?
Powder metallurgy can save 30%-50% of material compared to traditional machining ,no post-processing is required . It is a very cost-effective alternative with good surface finish and high dimensional accuracy . It has a huge advantage over traditional machining methods such as casting , and milling ,etc., .